by Dai
I'm a big fan of Brandbright coach kits. There is something about the proportions that appeal to me and they run superbly well. Somehow, I just can't reconcile myself to plastic coaches though I acknowledge that, on videos, they look fine. I suppose it's just a thing I have about plastic things. It always seems to me that they look just a little too well moulded and precise. This may seem like an odd thing to say, but I think it's that I want my stuff to be less accurate somehow, perhaps a little more obviously hand crafted?
Now, before I continue, I must say a word or two about this article. Many articles I read in magazines, supposedly designed to help and encourage me, do no such thing. This is because the writer assumes a level of technical competence in his reader or is afraid to teach Grannie to suck eggs. The result is that many such articles are absolutely useless to me; they might as well be written in gibberish. To continue the analogy, in model engineering and railway terms, this particular Grannie doesn't even know where the eggs are kept.
I make no apology therefore for what follows. There will be gibberish, of course, but, in case, dear reader, you know absolutely nothing and have been afraid to even open a Brandbright box, this article is for you. It is the article I wish I had been able to read when I began all this wonderful garden railway hobby.
A two compartment second class coach, complete in this case with telltales.
The other thing about building such a kit is the sense of achievement at the end of building it. I don't feel the need to design and completely scratch build. While there are chaps out there to do the planning and design donkey work, a kit gives me enough to do to make it mine. Just buying a coach off the shelf seems to me a very small piece of retail therapy. For me it works like a Chinese meal or a Big Muc. Building your own coach is more like turkey with all the trimmings. So with that bloated feeling in mind, and with the word 'turrkey' ringing in our ears, I will continue.
Laser cut parts are amazingly good to work with and Brandbright's brass and white metal bits are well made too.
Coach kit onlay. Note that I have yet to remove the droplight (window) frame, along with the spare piece separating it from the window recess. When I first saw these, I imagined that this extra fillet had some final purpose so lovingly kept them all safe! The droplight frames, painted separately push back over the glazing
First things first
The first job on opening the box is to identify the bits and read the destructions. This is the point at which I used to fail in the old days and I know many people reading this are like me. If you want this coach to satisfy you, it is the ideal opportunity to grit your teeth and do it by the book. Brandbright are very accommodating if you ruing them with a sob story; I love those guys to bits. Rarely do they mess up when assembling a kit of parts but it has happened to me once recently.
It is well worth the effort to run a piece of relatively coarse wet and dry along all the cut edges because they are scorched and will, the better, take paint once the loose black gubbins has been removed. I don';t find it necessary to remove all the colour; just the powdery bits.
Depending on th colour scheme, I now spray the wood with a primer. This has the effect of sealing the grain and, when it has really gone off, I sand down to a silky finish. The aim is to produce a grain free smooth surface onto which I can float a series of top coats.
But surely......?
...you will build the coach first? Not at all. The thing that matters the most and which consumes the most time is the drying of the various coats of paint. While I certainly flash off the coats to speed drying, each one needs to really go off fully before the next coat and certainly before sanding down. You can't accelerate the process with wood as you can when you bake loco parts in the oven by the Chris Bird method. You just have to allow the chemistry to work its magic in a warm room. In all that waiting for paint to fully set, that's the time to start to build the subframe and chassis onto which the final box is constructed.
I have found that the ideal way to inject the correct level of patience into the job is to build two coaches in parallel. That way, you stay busy enough to stop putting your eager grubby littel fingers on the paintwork. Incidentally, flashing off in front of a hot blower sure prevents dust and fluff spoiling the paint. So does the judicious use of a tack rag after rubbing down each coat.
Sanding
This might be a good place to talk about sanding down. The idea is to provide a stable surface onto which a top coat will bind and leave the surface finish you want with as few coats as possible. Where the final surface is to represent painted wood, is in the coach interiors, I don't mind a bit of grain showing through even though it is not to scale and actually, it would be invisible at scale distances represented by the 6 foot rule. As a long time miniaturist, I have a slight desire to show grain, even overscale, where it would normally exist. The outside of a coach is another matter. You would not expect to see any grain there. Because of that, I attempt to eradicate it before the top coat goes on. There are two options. One is to eradicate the grain at the primer stage and the other is to top spray, take a look, curse and bring out the wet and dry yet again. No prizes for guessing which method I have ended up with.
I use a small piece of quite coarse P400 wet or dry and, once the solvent pong is more or less gone from the coated piece, I lightly rub evenly all over. Now, if you are to avoid the divorce courts, do this on a sheet of newspaper, preferably unobserved, for, I kid you not, the fine dust you will create will go everywhere and stain for ever. No elbow grease here; let the sandpaper do the job and the end result will be even. Sand for twice as long as you really want to and then some more if you want this to be the last time you have to do it. If you are in doubt as to whether you have done enough, clean off with a tack rag (not a wet cloth!) and respray. Can you still see grain? I thought so!
But I digress.
Here, below is today's project; a full luggage brake. As you can see, I have primed the two different onlay sections and the plastic ducket too. I have yet to prime the coach side, which, to begin with, will have a full white coat
All the constituent wooden parts are sprayed with them lying horizontally and flashed off in front of a greenhouse heater/blower. This includes the onlays. If the final paint finish is to be a light colour, I use a white spray but where, in this case, the final colour is red, it will sit better onto a red/brown undercoat.
Where there is to be two tone, such as my beloved 'Blood and Custard', I use masking tape to end up with a two toned primed finish. This means masking up several times for each side panel but it is definitely worth the effort. I lie the onlay on the coach side and mark where the line between the two colours has to be, trying to get the join halfway under the horizontal bar of the onlay. That way, the join between the two colours need not be too neat since, of course, the bar will hide it.
I could use a primer/filler but I think that might bring problems of its own.There is a compromise to be had between using a primer that fills big holes and one that is wetter and thinner. I don't want to obscure all the engraved detail. I find the best primer of all is the white Zinsser which containes shellac. It must be very,very,VERY thoroughly shaken upside down to mix before use.
If you examine the picture below you will see that the patterns of planking and upholstery are acually burnt into the wood, not just marked out. On the left is the glazing spacer which goes between the outer side piece and the inner piece, shown on the left. The glazing perspex is ready cut and fits in the spaces exactly, in the same plane as the wooden spacer. This means that the 'glass' need not be glued. It is held securely in the sandwich.
You can also see that, as well as etching in the design, Brandbright has thoughtfully etched in the part number and its name and whether it is a left or right sided part. In the instuctions they make it very clear when you should glue the written on sides face to face to obscure the writing. I've used old stock photos of the internals of the Directors' saloon here. naturally, the luggage brake does not have upholstered doors.
Top coat Painting
I like the acrylic sprays that Halfords sell. I can't say I am overly fussed about authentic colours as such so my version of 'Blood and Custard' is Vauxhall Flame Red and Ford Gazelle Beige, Actually, since i first decided on these colours, Halfords have decided to discontinue the Gazelle beige so I have to buy it from suppliers online. If you are keen on specific colours, the staff at Halfords will allow you to pore over colour books and then mix you the very shade. You can buy it in a spray can or a pot, which is cheaper. The thing to realise though is that when they mix to your specification, what you get is not acrylic but cellulose based.
I always spray onto a horizontal surface until it is well wetted then flash off in front of a hot blower before transferring the touch dry piece into the house to properly cure.
Pictured here below are the fully prepared constituents for building the sides of the full luggage brake coach. From the top are the internals, then the glazing spacer, the solid side panels then the onlays and ducket.
I'm sure it makes sense to paint all the constituents before assembly and none more so than the internals. I simply cannot see how you can possibly paint these unless individually flat in front of you in a good light. Attempting to paint them once built would be extraordinarily difficult. I use Humbrol or Vallejo acrylics and as you will notice, below, it pleases me to add some of the dirty marks you would expect to find in a guard's van or luggage compartment.
The leather strap for raising the droplight and the stained wood has yetv to be given a coat of satin varnish to just give a slight sheen and the ventilators, which would have been brass, need a lick of gold follwed by a wash of sepia to bring out the detail. Silly really as few will ever see it.
Chassis
Brandbright have a rather neat way to ensure that the wheels stay square and true. They have you build the solebars by laminating two pieces together on each side. I build my coaches on a piece of glass so having applied the PVA I prefer to use, I approximate the two elements then pin them to the glass using sprung grippers. That way, I know the solebars will stay true when I come to glue them to the floor. Their final position is fixed by the headstocks at either end. Again, once I have applied a generous amount of PVA, I fix the whole floor assembly onto the glass as shown. Once the glue has set, the chances of warping are zero.
Before I fix the solebars to the floor, following Brandbright's instructions, I trial assemble the wood screws that will hol;d the axleguard castings into the tiny guide holes thoughtfully provided by Brandbright. It's wise to do this and then remove the screws before glueing because it will be very tricky to fix the aleboxes on at the very end of construction. This is because since the screw heads are inside the solebars you can't get a screwdriver directly onto them. Replacing screws that have once found a home in the wood is a lot easier. Why not assemble the axleboxes onto the solebars before glueing the solebars to the floor? Well, you could do that but you risk the possibility of glueing the floor asembly less than square. You wouldn't be able to use the clamp as I have in the picture below. In addition, the whole of the rest of the 'box' assembly would be on roller skates. Not good!
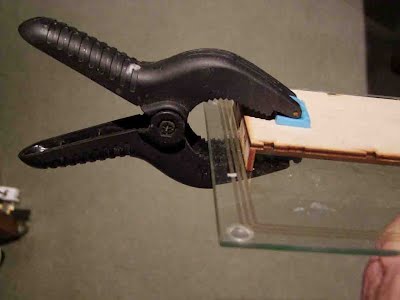
I find these clips absolutely essential for coach building but I also use them when glueing walls of a resin building together. Pinched onto one wall they stop the second wall sliding inwards The glass I use is actually a toughened glass place mat but shhhh.....nobody knows where it went! Here it is in use to fix the floorplate to solebars and headstocks.
Assembly
Once the sides and onlays are finished to my satisfaction, the coach can be build as per the excellent written instructions. I leave the onlays until the very last so that I can position them neatly in relationship to each other at the corners and ensure everything is free from gaps. I suppose that what I am saying here is that, however acurate the laser cutting is (and it is, very) there is still potential for some slop at the assembly point, what with the use of glues that occupy space. Adding the onlays last allows you to satisfy your eye and cover little discrepancies.
Assuming that the floor and the solebars have been glued together and are sitting squarely on my piece of glass, I first fix the ends, making very sure that the holes for theb buffer shank line up and that the ends are absolutely vertical. To make sure of this, I use a set square and only glue one end at a time.
For me, this is one of those moments in the build where you really do need to go away and do another job while the glue sets rock hard before you start the other end. The fixing of the ends is perhaps the single most important element to get right. Note that the floor and the ends have slots into which the glazing spacer will be fixed. Brandbright have thoughtfully made these irregular in size and position so it is nigh impossible to fit them wrongly. However, there may be a slight need for fine fettling to allow the 'box' you make up next to sit sweetly together before glueing. Again, time spent fiddling with it now is well worth spending.
Here, in the picture above, you see the glazing spacers and the central compartment divider assembled. I have found it best to do this using a generous amount of PVA, glueing it all at the same time. This would not be possible if the ends were not very solidly attached and if there was the remotest problem with the fit.
Roofing
I like to be able to remove the roof so that I can add interior detail at a later date or fit a set of lights. Brandbright make no allowances for this but it is not difficult to adapt what you get to make a removable roof easily enough. I use spare wood sprue for the ends and sides but on this occasion decided to add greater stability with a deeper led by carving suitable pieces from a wooden tongue depressor I happened to have lying about. Scrounge a few from your GP.
The roof is built in two layers which is just as well as they are flimsy and very prone to warping and twisting. Once the side pieces have been solidly fixed and the two layers are bonded with lashings of PVA, it makes sense if the roof is put onto the coach and held in place with elastic bands until the glue has completely gone off. This probably means several days. If you remove the roof before that, you will end up with a warped roof which may sit nicely on the coach even so, particularly if the transverse pieces are as long as those I used in the centre. This particular roof is a litttle warped because I did not wait long enough.
Waiting for the roof to set in its precise position is even more relevant if you like to cover it, as I do, in Solartex before painting. Solartex is a fabric which excellently mimics the canvas used on coach roofs. I prefer the black variety and I use a special tool, a small iron, to activate the adhesive and fix it to the roof surface.
Once the Solartex is fixed, I find that a spray of grey undercoat works well, particularly if followed rapidly by a smearing action to bring back the boriginal black of the Solartex in lines suggesting the action of rain on the roof.
After that, do you want lamps or ventilators? What is their purpose? Where would the go to do the job intended. With this coach, two compartments merit two lamps.
Bling
I love a little bling on a coach. Brass door handles and grabs of course and water transfers all provided in the kit. Also provided are a set of end steps and brass wiire to make the necessary handrails, one for the steps and one on the roof. Extra, but worth it, are the vacuum pipes and if you have those, you really ought to have a telltale system.
Note that, even at this stage, I have yet to fit the roller skates, leaving that task and the fitting of running boards to the very last. After all, a stable model is easier to work on and is less likely to find itself leaving the bench and making me cry!
Interiors
I'm sure a lot of us can't be doing with detailing the interiors of coaches and, to be fair, as they whizz around the track, you really cannot tell a coach with an interior from just a box. But, I'm a dollshouse man at heart so, for me, half the fun of this malarkey is the fiddling about. A luggage van needs luggage, or what's the point?
Coach lights are a joy at dusk and of course there is the pleasure you get showing the impressionable. All right, my grandchildren are the most important of these but there are others around whose eyes light up when you take the lid off. Those of a female persuasion then look pityingly at my wife, as if to say, 'Poor Dear, how do you cope with it?'
A brake compartment needs a brake wheel and a guard to operate it. Here, Sidney Street has a cosy little cabin where he can keep a watchful eye out through the ducket windows and read his copy of the Mirror too, Brandbright supply a letter rack so it seems mean not to fill it up. The brake wheel is a white metal casting I found on ebay by extremely good luck. A guard neds a red flag, not hard to knock up from plastic rod and loo paper soaked in PVA.
Why the bucket of coal? Well, sooner or later, I mean to fit a stove but I shall have to make one from scratch. The interior lights work and so does the rear lamp, powered from a battery box held by velcro under the chassis, between the wheels. What you can see on the top of the coach end is self adhesive copper tape which completes the circuits when the roof is seated down. As yet, this is an imperfect system but worth playing with I think.
So, there you have it, a nice sweet running Brandbright coach, Enjoyable and easy to make. Reasonably priced at £39.90 plus extra for wheels and couplings and bits of bling and I would say, once made, the level of satisfaction of ownership can't be matched by simply buying something off a shelf. It would be interesting to speculate on the resale value of such a coach but I would imagine you'd get your money back if you took your time and made it well. Go on, go on, go on!! You know you want to!